Totani Data Communication System vol.1
Introducing the main functions of
the Totani Data Communication System (DCS).
In this section, we introduce the main functions of DCS along with its screens.
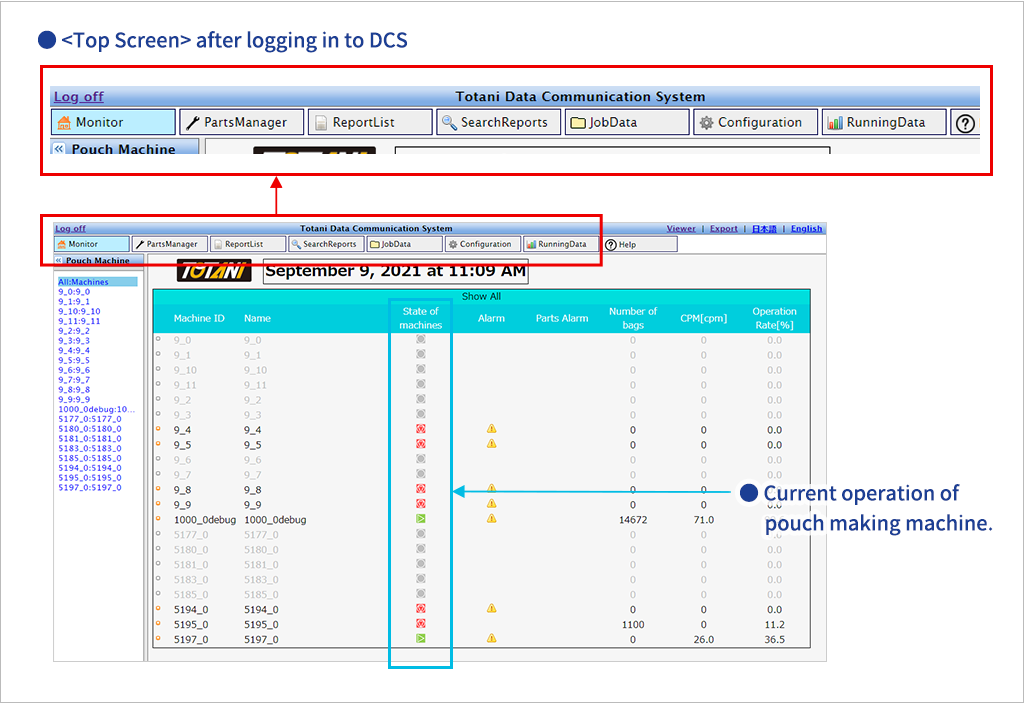
After logging into DCS from the login URL, the first screen displayed is the <Top Screen> shown above.
The header of the top screen has tabs that allow you to move to the function setting screens such as "Monitor (top screen)," "Parts Consumption Management," "Report List," "Search Reports," "Bag Making Conditions," "Settings," and "Operation Data".

About the DCS data that can be viewed on the top screen.
The current operating status (number of bags made per day, operating rate, and current shot count) of all pouch making machines connected to the DCS can be checked.
In the "Operating Status" column, you can check the operating status of the pouch making machine by using the symbols (e.g., the symbol
indicates that the machine is running and the symbol
indicates that the machine is not running) or by using a combination of the symbols and text color (e.g., the text coloris gray and the symbol
indicates that the machine is not connected or is turned off).
- [1] Monitor (top screen): Checks the detailed operation status of the pouch making machine.
From the top screen, click the "Specification Number" of the pouch making machine on the screen to go to the detail screen of the selected pouch making machine.
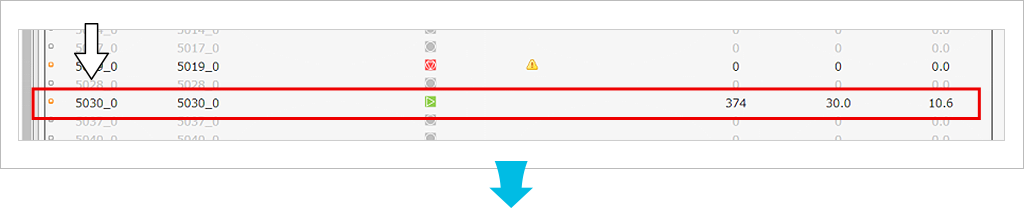
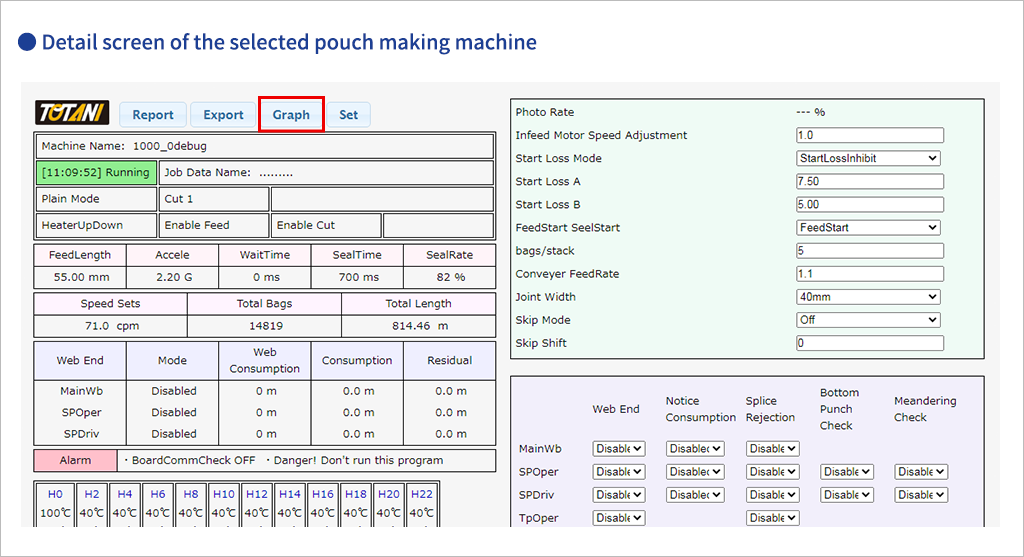
In this section,
- Prepare various pouch making status reports (Click on Report).
- Text/CSV File Export (Click on Export).
- Graphical display of data (Click on Graph).
- Export of pouch making conditions to pouch making machine (Click on set).
and other functions are available.
Right side screen of detail screen displays the current pouch making conditions for the selected pouch making machine. Important settings such as the servo operation status of the roll film section and cutter, heater temperature settings, etc. can be checked (* in blue border).
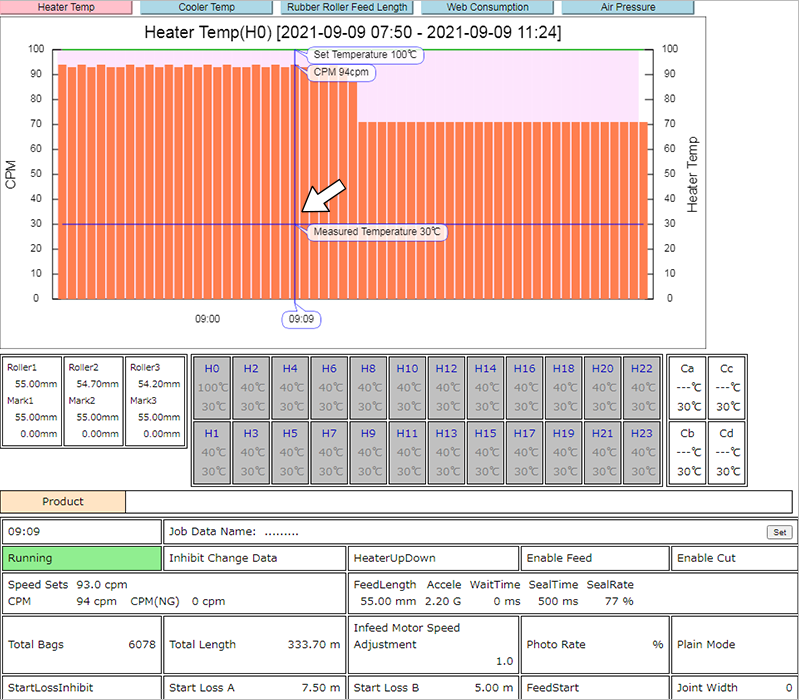
By clicking on the "Graph" button , the operating status of the selected pouch making machine today, from the start of operation, is displayed in a graph. Move the mouse cursor over the graph to see the bag making status at that time.
- [2] From the monitor (top screen) to the parts management screen.
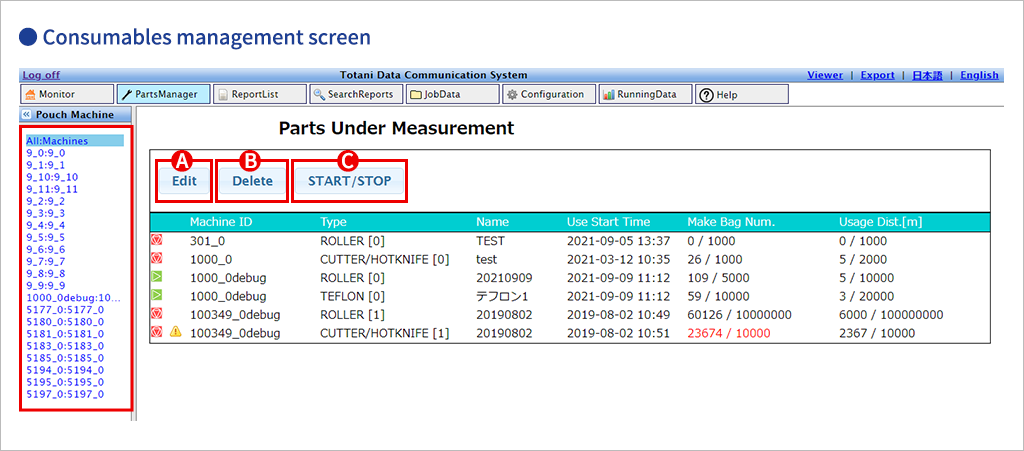
Selecting the "Parts Management" tab on the monitor (top screen) displays the "Parts Management" screen for the parts to be measured, as shown in the figure above. Here, you can measure the number of pouches made using the parts on the selected pouch making machine, as well as the distance of raw materials used.
The following items are displayed here.
- Measurement status
- Alarm (setpoint exceeded)
- Specification No. ・Type (roller, cutter/heat blade, punch, teflon, other)
- Number
- Parts name
- Start time of use
- Number of pouch making
- Distance used
- Set number of sheets
- Set distance
-
If there are further new parts to be managed, click "Edit" in
to bring up the edit screen.
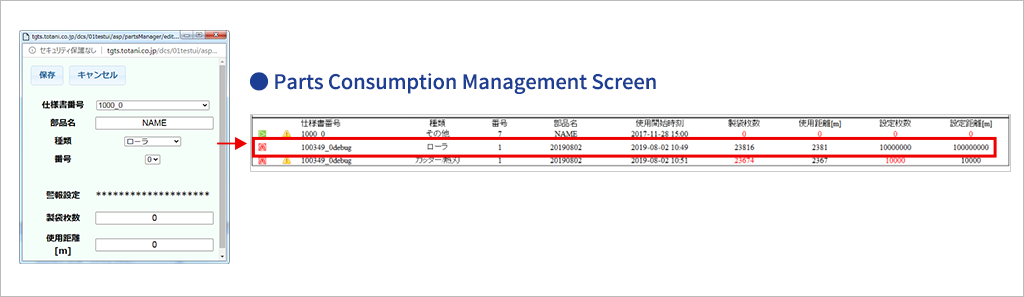
Here you can register a new part to be managed.
Enter the Specification No. , part name, number, number of pouch making, and set distance, then click the Save button, and the new part item will appear on the Parts Management screen.
For parts registered in the parts consumption management data, click
on the management screen to display the delete screen. From here, the data of deleted parts can be deleted.
You can also check the deletion history by selecting the pouch making machine specification number from the list on the left side of the management screen.
In addition, when "Start/Stop" of
is pressed on the parts consumption management screen, the following screen appears.
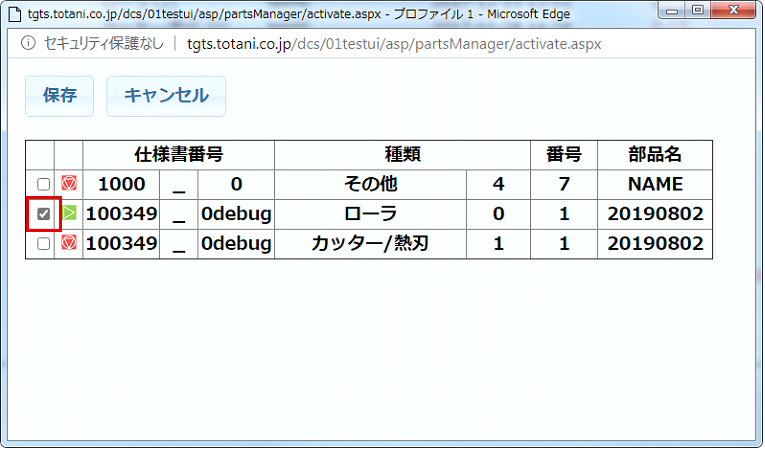
On this screen, operate the check buttons for the parts you want to measure or stop measuring, and press "Save" to apply the settings.
Continue to Functions of Totani Data Communication System (Vol. 2)
*The information on this site is subject to change without notice.